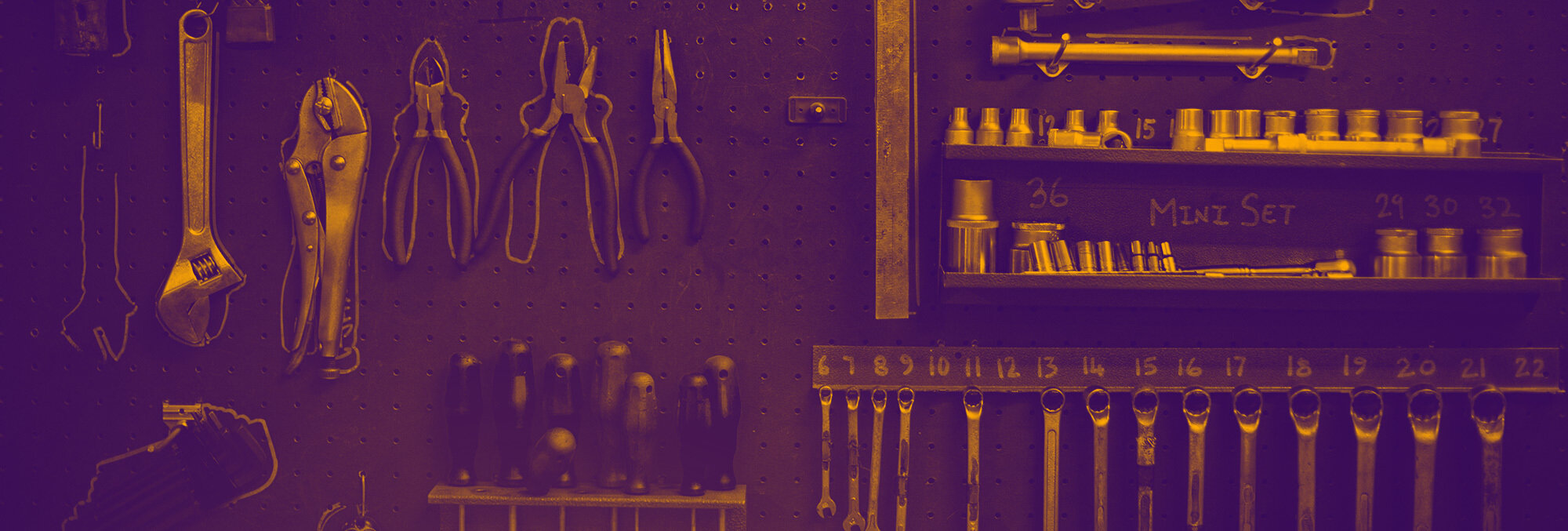
TECH TIPS
Turret Clutch Bolt
The old saying about “Lefty loosen, Righty tighty” does not apply to the large bolt and nut holding the Turret clutch together. This bolt and nut have “Left-handed” threads and requires (1) 1-1/8” wrench and (1) 1” wrench. Keep this in mind when trying to dis-assemble the Turret clutch.
The old saying about “Lefty loosen, Righty tighty” does not apply to the large bolt and nut holding the Turret clutch together. This bolt and nut have “Left-handed” threads and requires (1) 1-1/8” wrench and (1) 1” wrench. Keep this in mind when trying to dis-assemble the Turret clutch.
Turret Clutch Facing
When installing the assembly with UHMW or Nylon facings, the facings must be clean. Grease and oil can affect the amount of friction the facings can apply to the drive disk. Avoid touching the facings with your fingers as you install the disk.
When installing the assembly with UHMW or Nylon facings, the facings must be clean. Grease and oil can affect the amount of friction the facings can apply to the drive disk. Avoid touching the facings with your fingers as you install the disk.
Prevent Pinsetter Motor Failure
After months of no activity, pinsetter motors can have some major problems. The majority of these failures can be traced to the mechanical centrifugal switch. A single-phase AC motor has a centrifugal switch inside its case, attached to the motor shaft.
After months of no activity, pinsetter motors can have some major problems. The majority of these failures can be traced to the mechanical centrifugal switch. A single-phase AC motor has a centrifugal switch inside its case, attached to the motor shaft. The switch is closed when the motor is off and motionless. When you turn the motor on, the switch conducts electricity to a capacitor and an extra coil winding in the motor, increasing its starting torque. As the motor's revolutions per minute increase, the switch opens, as the motor no longer needs the boost.
If the centrifugal switch fails to open, the start windings in the motor will burn up. When this happens, the motor will not start. To do a quick check, remove the belts from the motor and turn it on. After a few seconds, you will probably hear a click. This is the switch opening, it does this when the motor reaches about 75% of its maximum rotations per minute. Turn the motor off. As the rotation slows, the switch will close. If you suspect the switch is sticking, you can send the motor out to be repaired or check the switch yourself. There are many videos online regarding this repair.
Setting Table Wedges
If you notice excessive movement of the pin holders, check the wedges that hold the levers onto the square swing shafts.
If you notice excessive movement of the pinholders, check the wedges that hold the levers onto the square swing shafts.
Switch Cluster Visuals
Using a wax pencil or white paint, highlight the embossed letters on the Switch Cluster to make them easier to see.
Using a wax pencil or white paint, highlight the embossed letters on the Switch Cluster to make them easier to see.
TS1 Actuator Arm Adjustment
Use a black fine tipped marker to make a reference line on the back of the adjustment plate.
Use a black fine tipped marker to make a reference line on the back of the adjustment plate.
Pins spinning on your T-Bands?
If you have a problem with pins spinning at the corners of the pin feed deflectors, try attaching a piece of poly cord to the ball cushion. Start with 1 piece and add 1 or 2 more if needed, working towards the kickback.
If you have a problem with pins spinning at the corners of the pin feed deflectors, try attaching a piece of poly cord to the ball cushion.
Start with 1 piece and add 1 or 2 more if needed, working towards the kickback.
You Can't Be Successful If You’re Hurt.
Safety is the number one most important thing to remember and practice anytime you are around a pinsetter or anything mechanical or electrical. The rule of thumb is to always DISCONNECT POWER to the pinsetter that you are working on before attempting to do any repairs or maintenance.
SAFETY:
Safety is the number one most important thing to remember and practice anytime you are around a pinsetter or anything mechanical or electrical. The rule of thumb is to always DISCONNECT POWER to the pinsetter that you are working on before attempting to do any repairs or maintenance.
There are various ways to turn a pinsetter on or off depending on the specifics of your bowling center. However, there is only one way to completely guarantee that power is not present and that is to unplug the main power cord that goes into the female receptacle on the top of the electrical box. Some people will turn off the main circuit breaker versus what we are recommending, but technically there is still incoming voltage present to the top of the breaker. Unplugging the machine is a 100% guarantee that you will be safe.
There are a number of things on a pinsetter that can potentially hurt the individual if they are not conscious of some simple rules of the workplace. Always make sure that you are not wearing extremely loose clothing when you are around a running machine. Jackets, sweaters and a variety of other types of clothing can get caught in moving belts, hang on hardware when you are trying to enter or exit a pinsetter, etc. Hair length is another one of those things that can be an issue. If you are allowed to have long hair, I can tell you from personal experience, tie it up or tuck it in a hat when you are around a running pinsetter. If your hair gets caught in a moving cross conveyor belt, I can tell you that it is quite painful and only had to happen one time for me to practice that safety measure going forward. The final thing most of us overlook is jewelry. It always a good idea to take off all your jewelry before working on a pinsetter. Not only do you risk catching your jewelry on something and possibly losing or damaging it, but you may also harm yourself if something like a ring becomes crushed and stuck on your finger.
AWARENESS:
To be aware is to be in control of not only your safety, but the environment that you are being asked to maintain. Pending your initial responsibilities as a pin chaser, try to be focused and aware of what should be considered normal versus abnormal. Many of the things that we have learned working in the back of a bowling center stemmed from what we were able to hear, see, and feel.
Listening can go a long way when it comes to catching problems before they become major catastrophes. Sounds tell you when you have a bearing failing, a loose or broken part, or something that is out of adjustment. There are normal operating noises and then there are the squeals, banging, crashing, and violent sounds. Make sure you learn the difference between the two categories.
The sound of a short turret belt “squealing” because the turret has not indexed for too long is a normal sound that is common in all bowling centers that have A series pinsetters. If you are behind a pinsetter that is emitting loud banging noises, that is a sign of a problem that needs to be addressed. A note should be left for the Chief Mechanic so they can attend to this issue as soon possible. When you have some free time in between your pin chaser duties, walk behind the pinsetters as they are running and listen to each one as you walk until you find the quietest one. That should be the benchmark for all of the pinsetters.
ENVIRONMENT:
Cleanliness is a critical factor that needs to be maintained in the back of the bowling center to promote a smooth and efficient operation. This should be an ongoing effort by the entire team on a daily basis. Ultimately, the cleanliness of the backend and shop area will be directed by your Head Mechanic if not the Owner. If things are organized, floors are swept, and things are put away, this promotes an efficient, safe, and organized environment.
I was taught growing up to always keep the runway clean and clear just like an actual airstrip. My mentor referred to the entire length and width of the floor behind the pinsetters as the “Runway”. We swept this every day and it was amazing what you would see sometimes when you came in the next morning. When the floor is perfectly clean and something falls out of the pinsetter or a bolt comes loose and falls on the floor, your eyes are drawn to it immediately. You deduce that since the floor is always clean this has to be from a pinsetter in the near area and you should start looking for where the part or bolt may have come from.
At the least, you can leave a note for your supervisor so they can do a complete and thorough evaluation. When the floor is constantly a mess and the runway is not clear you never have a base picture in your mind as to what it should look like. So always keep your eyes focused when you walk or sweep the runway.
Organization is the key to clearing a call or fixing a problem on a pinsetter in the least amount of time. Keep your tools organized and put them back after every use, preferably wiped down and clean. By making this a habit there will be no additional time spent thinking about where they may be. Bowlers do not like to have to wait longer that a minute, and in most times no longer than 30 seconds for a problem to be fixed.
The habits and recommendations throughout this document are made by everyone here at KPP because we have all had great success not only in machine performance but also within our career growth over many decades. Typically, great proprietors and business owners that have successful and busy bowling centers tend to follow this line of thinking in regard to hiring people, or at least that has been our collective experience. The better your work habits are, the faster you will have opportunities to learn and grow into a great Head Mechanic or Facility Manager.
We Thank You for taking the time to read this article and we hope it will be helpful in your journey forward.
Don Agent
Brand Manager, KPP
Transport Band Bearing Housing
If you remove either of the T-band bearing housings while doing maintenance, be certain to orient the housing correctly before reinstalling it onto the shaft. This is also a great time to have a machine shop place a small flat spot where the threaded rod goes into the housing. This gives the locknut a flat area to tighten on to.
If you remove either of the T-band bearing housings while doing maintenance, be certain to orient the housing correctly before reinstalling it onto the shaft. This is also a great time to have a machine shop place a small flat spot where the threaded rod goes into the housing. This gives the locknut a flat area to tighten on to.
Ball Accelerator Removal
Before removing the wires inside the accelerator control box, snap some clear photos of the wiring as a reference for reinstallation.
Before removing the wires inside the accelerator control box, snap some clear photos of the wiring as a reference for reinstallation.
Removing a Pin Holder
When removing the pin holder, undo the mounting nuts and slide the holder forward off the swing shaft. This will leave the mounting plate between the swing shaft and the wire channel which prevents the wire from being pinched during reinstallation.
When removing the pin holder, undo the mounting nuts and slide the holder forward off the swing shaft. This will leave the mounting plate between the swing shaft and the wire channel which prevents the wire from being pinched during reinstallation.
Pivot Bearing Change
Follow the chart in the manual and number the holes on your new pivot bearing before installing.
Follow the chart in the manual and number the holes on your new pivot bearing before installing.
Switch Cluster Cam Tip
Mark a line on the switch cam and the shaft. Paint, White Out, or even a wax pencil will work. This will enable you to see if the cam has moved and give you a reference point while adjusting the cam.
Mark a line on the switch cam and the shaft. Paint, White Out, or even a wax pencil will work. This will enable you to see if the cam has moved and give you a reference point while adjusting the cam.
Sweep Wagon Wheels off Track?
Remove the belt from the sweep motor to easily get your sweep wagon wheels back into the tracks.
Remove the belt from the sweep motor to easily get your sweep wagon wheels back into the tracks.
Changing a Pin Holder
When changing a pin holder, slide the clips for the wire channel cover against both sides of the pin holder. This will allow you to replace the pin holder in the same place it was removed from.
When changing a pin holder, slide the clips for the wire channel cover against both sides of the pin holder. This will allow you to replace the pin holder in the same place it was removed from.
Stealth Mode
Want to keep your center's machines operating smoothly? Use your ears.
Many noises are early warning signs of a failure to come. These warnings can be drowned out by the crash of pins
Want to keep your center's machines operating smoothly? Use your ears.
Many noises are early warning signs of a failure to come. These warnings can be drowned out by the crash of pins and the thud of bowling balls. Use the quiet part of the day and your ears as a tool for maintaining the equipment you depend on.
Test your equipment by going in early and turning on lane number one. Listen, shut it down, and turn on number two. Keep going all the way across the center, making notes on which machines sound as if they're tunneling to the center of the earth. Repeat the procedure, but this time cycle each machine. You can also do this from the service aisle behind the machines.
Run your lane conditioning machine without any distracting noise from bowling, television or music if possible. This key piece of equipment warrants attentive listening every day. Unusual sounds should be addressed immediately. Remember that Kegel tech support is available to help you with your lane machine 24 hours a day.
Try to determine what noises you are hearing and where they might be coming from. A plan of attack for this procedure is to go after the big noises first. The loud stuff can be covering up the softer noises that are just as important. Remember to listen to only one machine at a time.
Bearings, bushings, belts and clutches will "talk" to you if you take the time to listen. Motors and solenoids also have a dialect that can be interpreted as an upcoming problem. A buzzing relay should put the buzz in your ear as to its condition. The equipment will tell you what needs to be checked. With practice the language gets easier to understand.
To help with the mental part of this preventative maintenance procedure, think of it as a "search and destroy" mission. Hunt down the noisemaker and repair or replace it. The quest may be different on each machine, with similar sounds having several different causes. You may have to remove belts or unplug motors to assist in the search for the offending component. A mechanics' stethoscope can help track down noisy bearings.
Before starting this diagnostic procedure, stock your shelves with the appropriate oil and grease needed. Spare bearings, clutches and other parts should be on the shelf and ready to install. An oil can with a long flexible spout, along with a good grease gun with needle tips make things much easier.
Be prepared to spend some time taking apart complicated assemblies. Squeaks and rumbles can come from bushings and bearings buried deep within the machine. The sound of a drum solo from a pinsetter could mean an hour or two of "belly work" on a pit.
Various rollers, mounts and drive mechanisms can go from working condition to failure overnight. Urethane can become brittle with age, causing a purring machine to roar with disapproval when customers arrive. Belts and pulleys can be a source of noise. Check for proper tracking and tension. Belts with a glazed surface can make an annoying squeak and should be replaced. Inspect pulleys for wear. A mirror-like surface on the inside of the flanges can make a noise that can be mistaken for a bad bearing.
Motors can be a big contributor to the sound coming from the machine. Many have bearings that can be greased without disassembly. If you are not familiar with the proper procedure to grease these motor bearings, consult a local motor shop. Over greasing can lead to failure of the motor!
A noisy gearbox can be an expensive undertaking. The parts and hours involved with rebuilding a gearbox can take a bite out of a center's maintenance budget. The fact that the sound is coming from such a key component demands that it be repaired before it becomes a major breakdown during the league season.
Listen to the ball lifting mechanism on the approach. Some can be completely silent when idling and make a lot of noise when lifting a ball. It's very important to keep this part of the center as quiet as possible. The bowlers are nearest to this equipment and it can make a huge impression on them. The hand dryer should not sound like an F-18 fighter jet warming up for takeoff. Some of these motors have small bearings that are replaceable. Also check the fan itself to see if it's hitting the housing.
Listen to your air conditioning units as they cycle off and on. If it sounds as if a compressor is laboring to start up, check it out. Blower assembly bearings can make some serious noise if not lubricated. The exhaust fans in both the restaurant and restrooms are often overlooked, flip the switch and listen for possible future problems.
Refrigerators and coolers should run without much noise. Listen to them as they cycle off and on. If something sounds “weird”, check it out or call a professional. Nobody wants to walk into the center one morning to be faced with hundreds of dollars of spoiled inventory.
This is a good time to give your sound system a test. Listen for bad speakers, poor balance and distortion when the volume is turned up to late-night levels.
By enacting "Operation Hush" two or three times a year you can keep your center quiet and help get your machines running in top-notch fashion.